Of the many vague repair terms that float around in polite discussion, Overhaul is probably one of the most misrepresented and misunderstood. The primary reason for this fuzziness in the meaning is the same issue that both follows and leads most bits of repair terminology: There is no standardized nomenclature. This is clearly an example where context matters and if one were to ask 10 technicians to define their “overhaul”, it would result in 12-15 different answers.
It is important to remember that every technician is going to do things differently, value different things, and have different priorities. This will create differences, sometimes vast and significant, in what goes into an overhaul, how long it takes, and how much it costs. Some process details one technician includes as a matter of course may be omitted or require an extra charge from another tech.
For the purposes of this article, I will be writing from my perspective of a technician working on high-end and hand-made woodwind instrument for some of the most discerning musicians in the world. However, I also came up through the trenches of band repair shops and school band repairs, where a very different definition of Overhaul may be applied. Since it is from my perspective and experience, there may be some things other techs disagree with. I invite them to either subscribe and start a discussion in the comments or to write their own articles.
The Definition of Overhaul
Fundamentally, an overhaul is a soup-to-nuts repair of the instrument. How many courses are served between the soup and nuts is up to the individual shop. At a minimum an overhaul will replace all of the non-durable materials on the instrument, including pads, corks, felts, regulation material, and joint corks. How much more than that is done and included in the price is subjective to the shop. Most importantly, the detailed definition of overhaul depends on the level of the instrument and any specialized focus of the shop employed. A soup-to-nuts repair on a student saxophone is a completely different task list than what is required on a professional saxophone, much less other more highly refined woodwinds.
Let us separate the two camps: Student instruments on one side of the gymnasium and Professional instruments on the other, dodge balls at the ready. This separation of grades of instruments in itself is a bit murky, but we will approach it in the most general sense. As always, communication with your technician is crucial. Make sure your understanding of the job is the same as their understanding so you get and pay for what is appropriate and best suited to your expectations and needs
.
For many years, and even still today, the term Overhaul when referring to a student instrument has 2 stages of interpretation. First, there is the Repad, which generally means replace all of the pads and corks and sundry other things related to playability. The Repad is the way the majority of band shops refer to the soup-to-nuts treatment. The Overhaul, when speaking school band tech parlance, is a repad plus refinishing—generally relacquering on saxophones. Occasionally shops would refer to plastic clarinets, piccolos, and oboes as needing a repad and wood body instrument as needing an overhaul to account for the oiling treatment often applied to the wood. Student flutes generally have no real differentiation since it is very rare (and far from cost effective) to strip and replate a student flute.
For the class of Professional Instruments, the term Overhaul is generally an abbreviation for Mechanical Overhaul. Soup-to-nuts applies to everything short of doing anything to the finish (except maybe hand polishing). Redoing the surface finish of a professional instrument (being the main definer of “Overhaul” in general shops) is rare among upper level instruments, so just “overhaul” is used unless it is a shop where they handle all types of instruments and want to remove ambiguity.
Overhaul vs Repad
As mentioned earlier, in a general sense the job performed on student instruments ia colloquially called a repad and on professional instruments is called an overhaul. Occasionally you will find the term Repad in the world of professional instrument repairs. This can get in to a very sticky area of particulars but I will summarize my application of the terms as an example.
In my shop a professional level mechanical overhaul requires scrutinizing and resurfacing toneholes to a degree of geometric and planar precision that surpasses what the makers provide on a new instrument. The precision of key fit is often corrected and improved to be tighter than factory new condition. These 2 mechanical details are far more durable than pads and bumper materials and should not need to be revisited again as often. With this in mind, when I see an instrument I have overhauled before, it may be able to get a repad where such mechanical features are inspected for soundness but the hours and hours an overhaul required for their proper set up is not needed. I have already done that work. Beyond that example, I do not perform repads in my shop. People come to me for the high precision I bring to the table and the only way to provide that consistently is to touch, inspect, evaluate, and improve every mechanical component, mating surface, and connection on the instrument.
In years past I used the definition that a repad returned the instrument to factory specifications and an overhaul established my specifications. I have since abandoned that practice. Almost universally, the mechanical aspects of a professional instrument can be improved from the factory standard. Many professional saxophones and clarinets can undergo significant and substantial improvements to the factory standards. In the case of handmade flutes and oboes, the improvements that can be done are minor, but still can be done to great benefit to the player. To ignore these places where improvement could be made would require compromise. As we know, the art of music making can be uncompromising. From having the proper tone quality, to the shaping of a line, to the proper attack and articulation, to even playing the right notes, where is there room for compromise? I view my approach to mechanical precision in much the same way. I can’t hang my reputation on compromises.
What’s a Student level? What’s Professional? What’s in between?
This is a topic for a whole other article where I may cite specific brands and models as examples. When in doubt, ask your tech. Not all instruments of a certain category are on the same quality. Never base an instrument’s categories on features. A high F# key on a saxophone does not denote a better quality instrument on its own. Likewise, a B foot or open holes on a flute can still be a student level flute.
What matters is the acoustic refinement, the quality of the build, and the precision and accuracy of the fine details. Aside from how the instrument plays, these details are often opaque to the player until it gets to the shop with a problem.
In the broadest possible description, student level instruments are mass produced, designed to allow the greatest number of beginning players to achieve success, and have fairly loose tolerances. Professional level instruments should be extremely precise, highly refined, and very accurate in their mechanical implementation. There can be very precise and accurate student level instruments and very loose and sloppy professional instrument. Every instrument is made by human beings who have good days and bad days. But there are some places were design or construction is an outlier on either side of the scale.
The weird grey area is in the world of intermediate instruments. This can be a vast region of misunderstanding and misnomers. Every tech and player may have a different understanding of such instruments as far as quality and what treatment they should get. Some intermediate instruments lean more toward the student side of the scale and some lean toward the professional side of the scale.
Precision, Accuracy, and Tolerance
I have thrown around these terms a bit and some may be scratching their heads over them. What do they mean? How do they relate to mechanical details? Why do they matter? I will admit I may use some of these terms with a bit of liberty that strays into the zone of not being correct, but I will explain my applied definitions briefly. I will have another article on this in more depth in the future, but here is a synopsis.
In a pure engineering or statistical sense, accuracy is the measured or observed difference from a true value. Precision is the repeatability of results. You can have precise results that are not accurate and accurate results that are not precise. Many people (including me) tend to mix up these terms.
One term upon which both can rely is tolerance. In mechanical speak, the tolerance is the extent to which a measurement of a part can deviate from the nominal size. An example of this could be in how a hinge rod fits in a key. On a student model instrument a hypothetical tolerance of 0.002” between the steel outer diameter and the key inner diameter (obviously the steel being smaller) may be acceptable for function. On a nicer instrument 0.002” is far too loose and a tolerance of 0.001” may be needed. On the highest quality mechanisms the tolerance is often 0.0005” or smaller to provide proper function of the mechanisms.
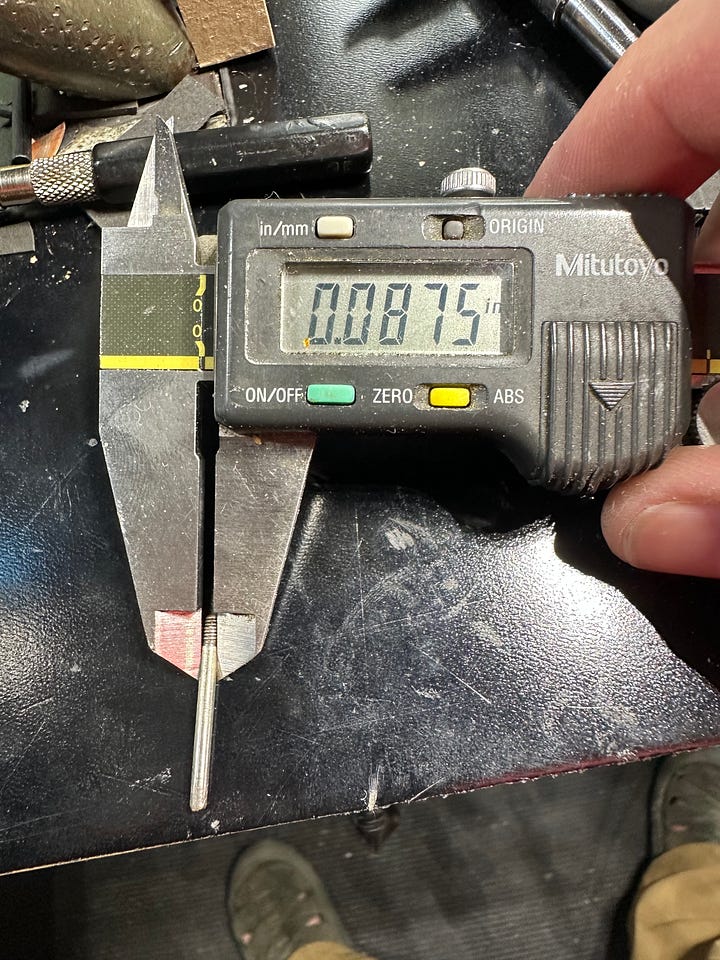
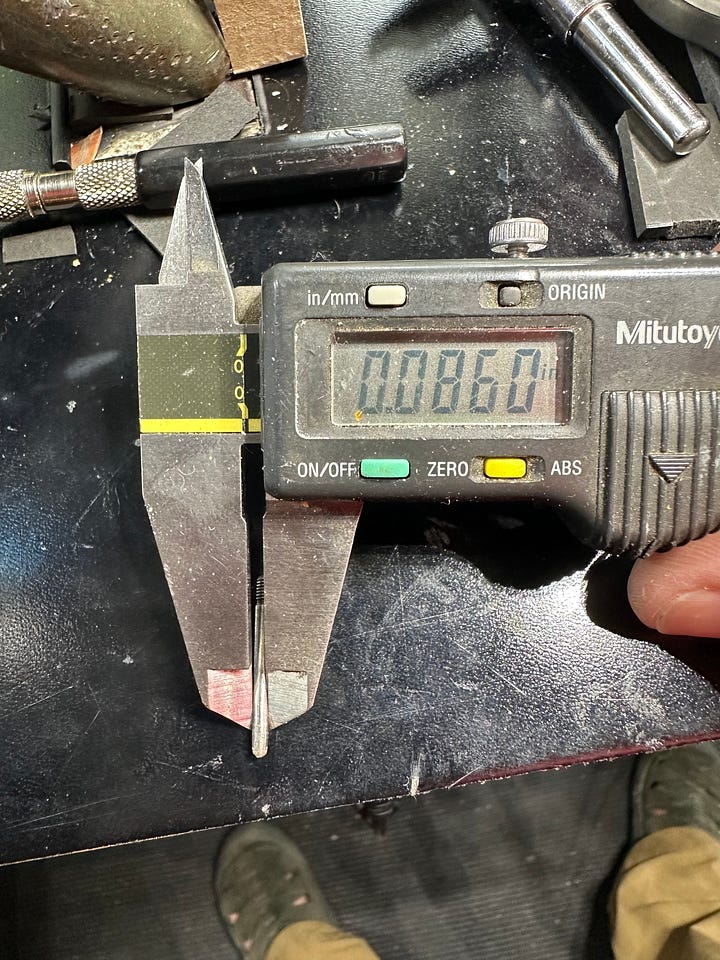
So, precision and accuracy can be bandied about —correctly or incorrectly— in a vague or subjective sense and people will get the concept of what you mean if you say something is more accurate or more precise. Tolerance, on the other hand can be a bit more difficult to talk about in vague terms because it is a concrete value. You need to know what that value means in the context of the system you are discussing for it to be understood and appreciated.
For the differences in overhaul jobs, just remember that nicer instruments require tighter tolerances. Without tight tolerances, the mechanisms simply will not function as they should. Lower grade instruments can function with looser tolerances. Establishing tighter tolerances on them may improve performance or it may be a waste of time and effort.
Time is Money, but Sometimes Not
Overhauls on professional instruments can be expensive and it can be a significant investment, especially for professional teachers and gigging musicians who don’t get paid all that much. You want to spend your money wisely so make sure you do your homework and evaluate your expectations.
As I mentioned before, some technicians will perform mechanical overhauls to factory specs. They will process these overhauls in a reliable amount of time, usually 15-20 hours of bench time and bill accordingly. This may be perfectly fine for your needs and expectations.
Others (like Jeff’s Woodwind Shop, for example) will work to exceed the maker’s specs and set into an overhaul like a hound dog with a slobbery rawhide and never let it go until it is right. Making it right is more important than getting it done within the billable time allotted.
Technicians like me work on the mindset that while making money is good and often required in today’s society, our professional reputation for going that extra mile and making it right for the player is far more valuable and important to sustain. This standard could be attained in a 16 hour overhaul, reconciling the math for the overhual price vs. time, or it could take 26 hours, or 36 hours with obsessive tweaking and tinkering to chase out all of the gremlins from their hiding spots. The price is rarely elevated much from where it was originally quoted despite taking 1.5-2-2.5x as long, and technicians like me are ok with that (kinda sorta). We would love to get paid for every hour spent, but the brutal reality is a $3000-4000 overhaul is not a terribly marketable service.
The topic of overhauls on woodwinds is wide and varied. Make sure you and your technician are speaking the same language and have similar expectations to make the process go more smoothly.
At the Woodwindfixer’s Bench is a publication of Jeff’s Woodwind Shop, a repair shop in Baltimore, MD catering to professional woodwind players. Jeff will be releasing his 2026 Overhaul schedule soon. If you want to be included in the notification, visit www.wwodwindfixer.com and send him a note.
Thank you for writing this article. As a technician who has shifted to pro work nearly exclusively, it's difficult to work on student model instruments, now. I've struggled with wanting to pursue preciseness in all my work knowing that I'm wasting time in the realm of student models. However, they can be an opportunity to try a technique I may want more experience on. Currently, I think I'm at the cusp of not doing any more student level work.
My main struggle is the price differences of professional to student work. I'm still figuring out how much time to estimate when adding key fitting and tone hole leveling and improving the mechanisms, etc... I'm still not sure I'm charging enough.
I enjoy your articles and I look forward to meeting you one day.